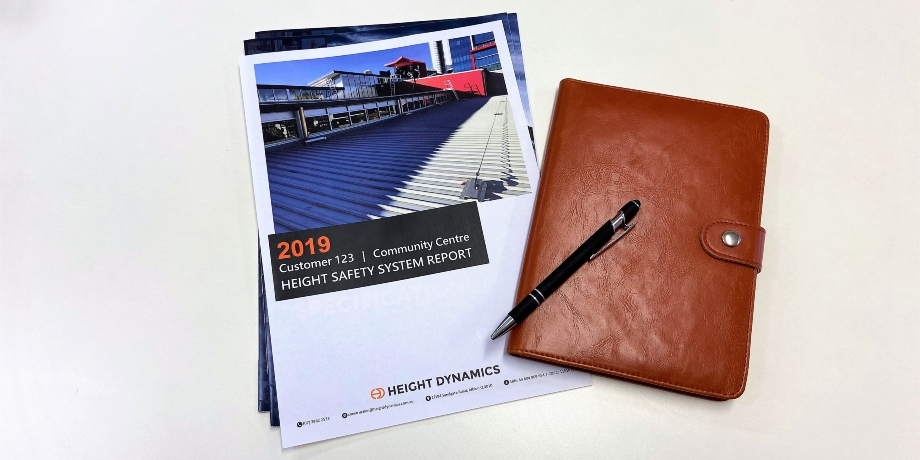
What documentation should a height safety system installer provide?
Providing a height safety system involves more than just the installation of products.
Specific documentation must also be provided.
So, you have had a height safety system installed. The system design takes into account the legislative and manufacturer requirements. Additionally, the installers have considered site specific conditions and ensured safe access to the system.
Done and dusted, the installer packs up, maybe leaving you with a business card and a promise to be in touch in 12 months when the system is due for inspection.
Safety system installations don’t end with the install!
But that is not all a height safety installation entails. On the contrary, it is only the first stage of the install.
In fact, at this point, without documentation the system cannot even be used!
The necessity of a height safety system report and operating manual is paramount. The report must include the manufacturer’s installation guide and substantiating evidence that the fittings or systems have passed legislative requirements. This is outlined in Sections 187, 193, 195 and 306I of the Work Health and Safety Regulation 2011 and Section 22(4) of the Work Health and Safety Act 2011. Section 198 of the Work Health and Safety Regulation 2011 also outlines that this information must be provided by the supplier/installer of the plant.
Documentation that you must receive by law
The system operating manual should include:
- A system layout/s identifying areas of building or structure that will be accessed by the safety system. That is, an anchorage plan and/or rigging layout.
- Identified “no-go” zones, for instance fragile surfaces or telecommunication equipment.
- Information regarding the system component identification and rating.
- System component testing documentation in compliance with Australian Standard 5532-2013.
- System user instruction and competency requirements for all potential users.
- Any additional system specific personal protective equipment (PPE) requirements, such as specific lanyard lengths.
- Information regarding inspection intervals and certification periods.
- Information regarding potential hazards and risks associated with the system.
- Emergency procedures (if applicable).
- Engineering certification of any structure that will be used as a part of the safety system.