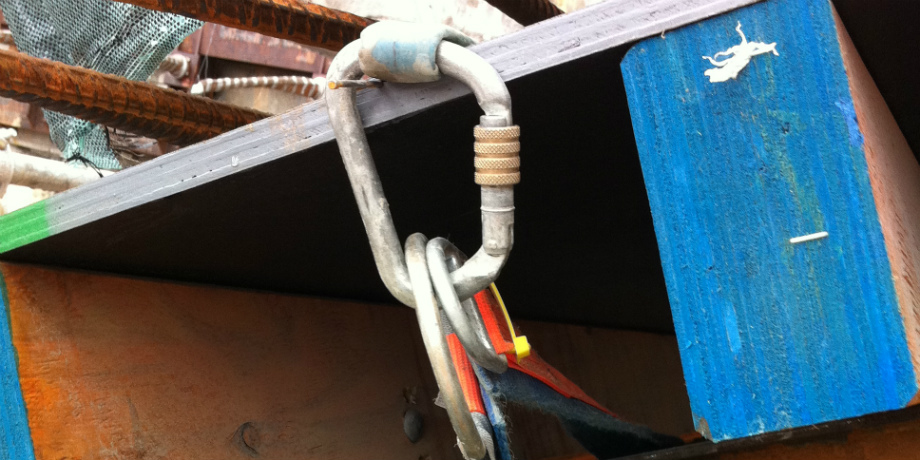
I was recently given the opportunity to walk around the work site of one of Brisbane’s major infrastructure projects. The safety team had asked me to take photos and provide feedback to them on my observations. The misuse of safety equipment onsite constantly amazes me. Some of the images are shared below.
End anchors of temporary static lines need to have a minimum rating of 25kN (about 2.5 tonne). Some static lines that are available on the market require as much as 30kN when two persons are using the system.
The main image shows an end anchor for a static line. Those who use carabiners a lot will recognise the misuse. For those who don’t, a 50kN carabiner cross loaded like this could have an ultimate tensile strength of less than 20kN. A carabiner is designed to be load along the length of its spine only. Any cross loading reduces the strength dramatically.
![]() |
![]() |
All mechanical or glue in anchors used in height safety must be proof loaded and meet manufacturers requirements.
The end anchor shown in the images above is creative but a poor attempt at making a reliable and solid fixing. There is only a single screw in concrete bolt that only has half its head holding the plate down. Is the bracket rated to 25kN?. Unlikely in this configuration), and guess as to where the workers were working? Yes! on the same side as the hammer. There is a high likely hood that the bracket could slip off the bolt in the event of a fall from the users.
To illustrate my point to the qualified rigger that installed this anchor I proof loaded a few of his concrete screw anchors with our hydraulic tester. One of the anchors pulled at 7kN or 700kgs, hardly a vote of confidence.
The failure of the anchor at 700kgs is particularly pertinent when you have as look at the photo below. It is a little difficult to see but two temporary static lines are terminated in the same bracket and pin and relying on untested bolts. The engineering requirement for this would be 2 x 25kN. Over 5 tonne! Given that the test that I performed on the screw bolts was 700kg, 5000kg will be difficult to get. The bracket was also placed on an angle which puts more force on each individual fixing.
![]() |
![]() |
The image above shows a double lanyard that was being used by one of the workers onsite. I am not sure how he missed the 20mm tear in one of the webbing arms before he used it. A brief inspection of this item would have made it obvious that this is not fit for use and should be condemned.
The Australian Standard AS/NZS 1891.4 Industrial fall-arrest systems and devices – Selection, use and maintenance clearly states that equipment to control the risk of a fall from height must be inspected before use by the operator.
Working at Heights is a high risk activity that needs to be actively managed. Lack of administrative controls had led to equipment being randomly left around on the site. Workers would literally search around and then pick gear up off the ground when they were required to work at heights. I suggested that a sign in/out system of control was required to ensure that the equipment was regularly inspected prior to use. This administrative control would mean the equipment would be available when required, and then rechecked and monitored when returned.
These images are a small snapshot of what I have seen over the years. The misuse of equipment either through ignorance or just plain laziness is astounding. Most of the people using or rigging these systems have been trained to work safely at heights.
The question begs to be asked, how effective is the training they have been getting. I guess that just opens another can of worms.
If any of these images look like the equipment or systems used on your site. Or, if you have any concerns about your working at heights procedures contact Height Dynamics.