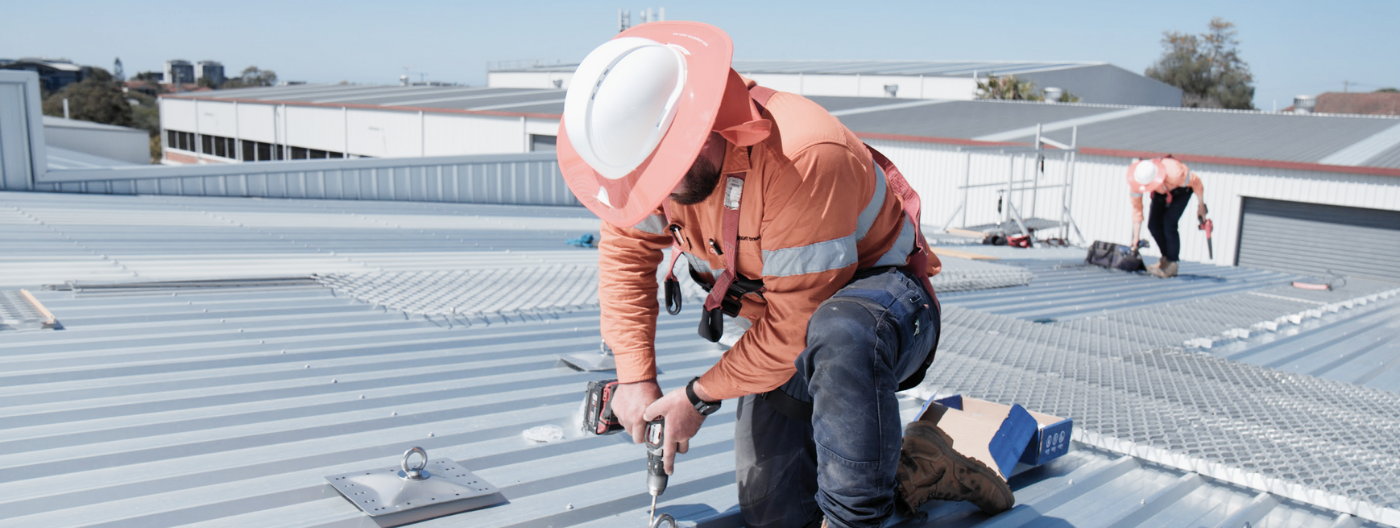
What training, qualifications, skills and experience do you need to become a height safety system installer in Australia? Let’s find out.
A high stakes, high responsibility role
Designing and installing a safe and compliant height safety system is an enormous responsibility. And that’s because working at height is considered a high-risk activity – with falls from height being responsible for more than 10% of workplace fatalities across Australia every year.
Newly introduced Workplace Manslaughter Laws raise the stakes even further. There is now direct responsibility on the shoulders of employers – and those with work site responsibilities – to provide for everyone’s height safety. Failure to do so may incur significant fines or even jail time
All of which puts great scrutiny on the work of height safety system installers.
No nationwide qualification and/or licensing regime
Despite the risks and responsibilities of the role, there is no formal course or officially-recognised qualification or professional licensing regime for becoming a height safety system installer in Australia. This is a gaping hole in our regulatory framework, and one we hope is eventually closed.
Must still meet local licence and regulatory requirements
In lieu of a national framework, there are national and local work health and safety regulations that must be adhered to in every Australian state. For the installation of height safety systems, these typically include the provision of detailed installation and compliance documentation, user manuals and instructions.
There may also be State-level licence and/or permits required. For example, in Queensland a current Queensland Building and Construction Commission (QBCC) Licence is absolutely mandatory for the installation, inspection and re-certification of any height safety system. This QBCC Licence must also be issued at an appropriate level. A Painter Licence is not adequate – however a Builder Low-Rise, Builder Medium-Rise, Builder Open, Structural Metal Fabrication and Erection or Carpentry Licence is sufficient.
Whilst we’re not aware of other States requiring the equivalent of a QBCC Licence for height safety system installations, things can change. So be sure to familiarise yourself with local State regulations and obtain any relevant licence and/or permits required.
Role requires high levels of height safety competency
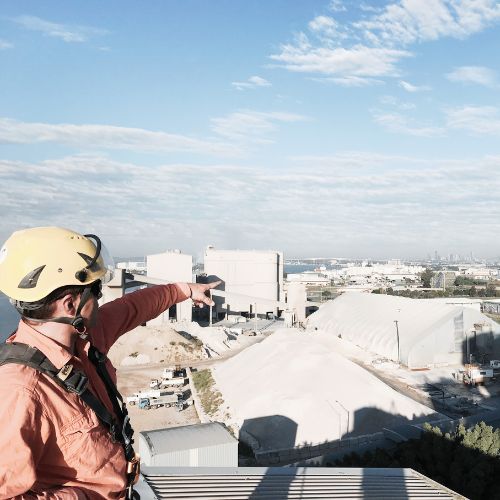
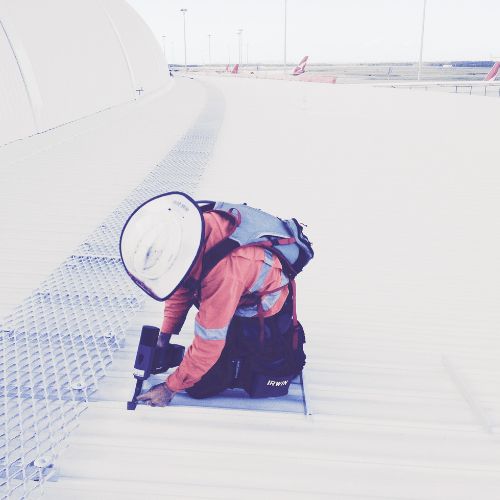
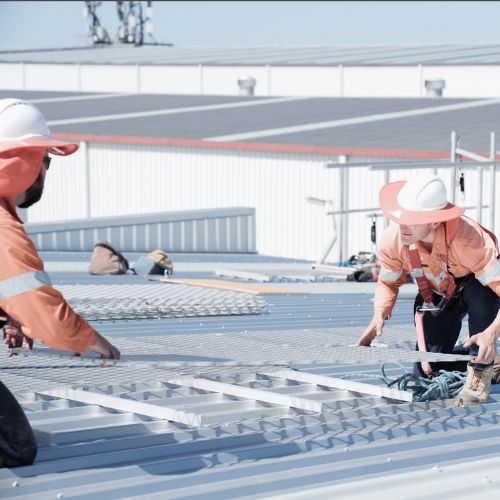
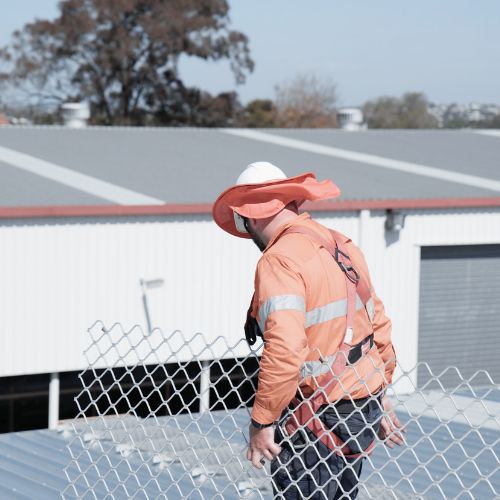
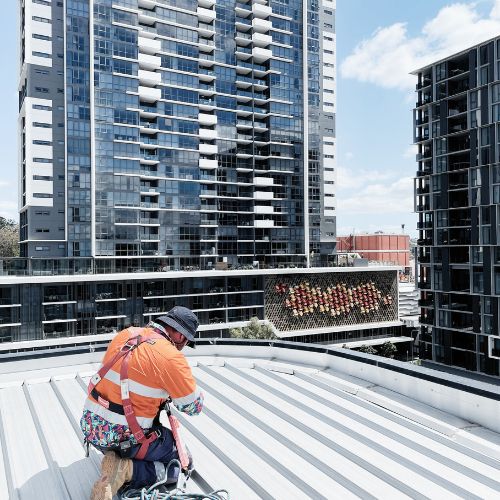
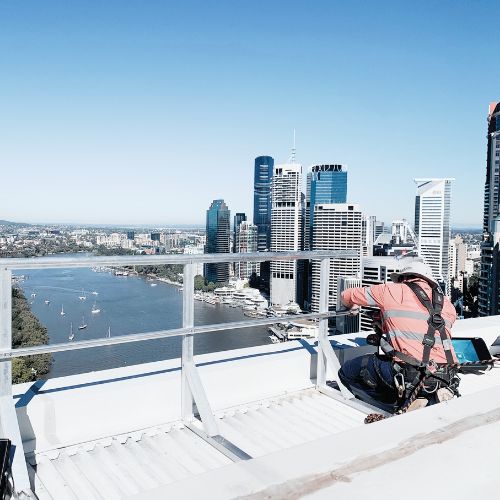
The lack of a national framework does not mean there aren’t significant height safety competency requirements for this role – in fact, quite the opposite. Being a height safety system installer requires some of the highest levels of training, skills and experience in the industry.
That’s why it’s essential to self-regulate and set standards for becoming a height safety system installer that go well beyond any minimum requirements. In this article, we will outline what those standards should be. For more personalised advice, feel free to reach out to our Installations team.
Must complete advanced height safety training
The Australian Standard for Industrial Fall Arrest Systems and Devices – AS/NZS 1891.4 (2009) – provides guidance on height safety training and competency development. The Standard outlines five progressive levels as follows:
(01) Height Safety Theory
Basic height safety theory for all people associated with harness-based work at heights. At a basic level it is pitched to operators up to and including supervisor level, to height safety technologists and to equipment inspectors
(02) Height Safety Operator
Training in the skills needed to perform harness-based work at heights under direct supervision of a height safety supervisor
(03) Height Safety Supervisor
Training and assessment in skills needed to perform harness-based work at heights unsupervised, to supervise entry level and other operators, and to participate in first responses rescue
(04) Height Safety Equipment Inspector
Training in the skills needed to detect faults in equipment and to determine remedial action
(05) Height Safety Manager
Training for people involved in the selection, design, manufacture or installation of height safety systems or equipment, or the development of control measures or work practices, in the technical skills appropriate to their tasks together with, as appropriate, training in risk management and systems management
As you can see, regulatory guidance suggests height safety system installers require advanced height safety training. And that should be no surprise. Once installed, a height safety system can be in-use for well over a decade – and every single time, any failure within that system could prove fatal.
Whilst height safety specialists like ourselves offer work-at-height training programmes (to inspector level), much of the above requires on-the-job training and skill development, typically under the tutelage of an experienced height safety professional.
Develop design skills through on-the-job installation experience

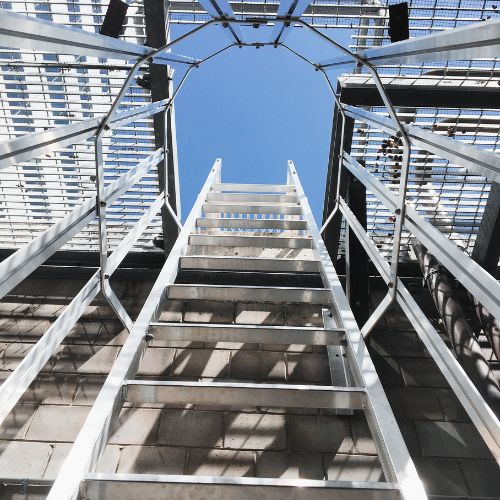
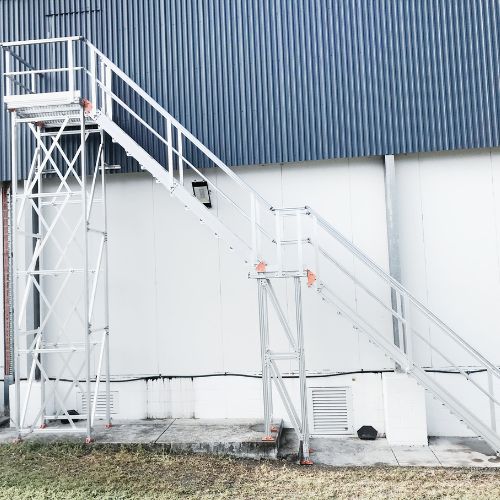
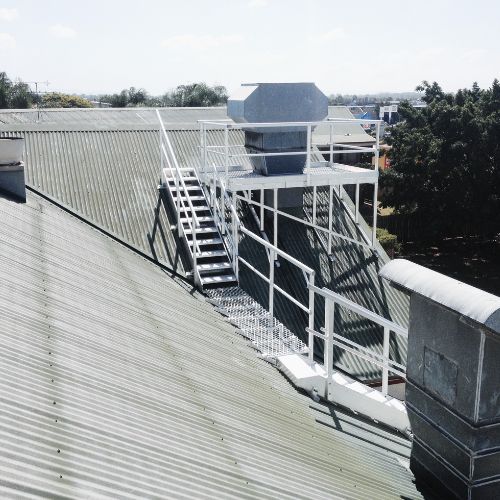
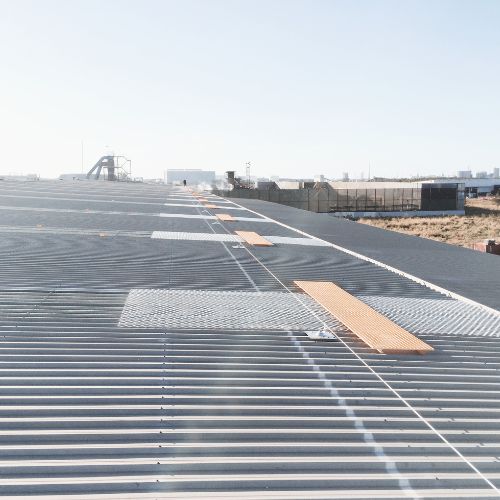
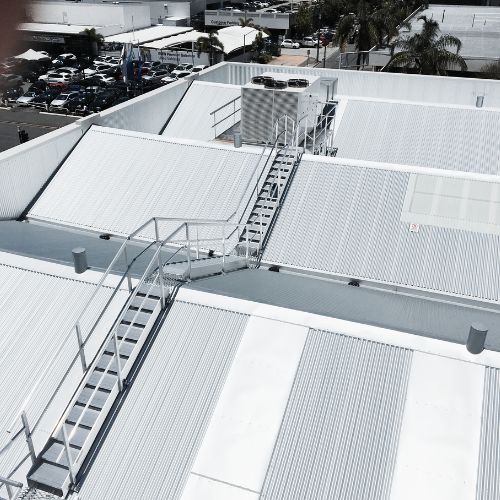
Every height safety system installation is different. The design has to cater for users performing specific tasks across a unique work site. The installation has to problem solve for any site risks, hazards and environmental conditions. Height-safe principles apply, but one size does not fit all.
That’s why plenty of practical, hands-on design and installation experience is a must have. Learning to evaluate a variety of installation scenarios. Working with clients and users to create informed, safety-first designs. Identifying the best components for your system and knowing how to apply these correctly. Installing, testing and documenting an effective, safe and fully-compliant new height safety system.
Do this repeatedly and on increasingly more complex installations (always under direct supervision of a height safety professional).
Always complete manufacturer’s training or accreditation
Nothing is more crucial to the successful installation of a height safety system than following the manufacturer’s instructions meticulously and to the letter. This applies to every individual component of the system.
Doing this may require the completion of the manufacturer’s training and/or an accreditation process prior to installation. For a multi-faceted installation, this can mean quite a lot of work upfront – but it’s necessary and worth it.
In our role as independent height safety inspectors, we continually come across dangerous, non-compliant height safety installations. Many are the work of professional height safety system installers who’ve failed to follow instructions correctly. In doing so, they’ve left users unknowingly risking their lives every time they use the system (which may have been in place for years by the time we see it).
Professional indemnity and/or liability insurance is recommended
Every height safety system installer should have sufficient and appropriate professional indemnity and/or professional liability insurance in place. This insurance is designed to protect you from future claims and/or liability in a variety of scenarios. Seek professional advice before purchasing.
Don’t want to leave your team’s height safety to chance?
When lives are on the line, there’s no substitute for experience. The Installations team at Height Dynamics have spent the last 20+ years designing, installing and inspecting all kinds of height safety systems. We cater for industrial, commercial and geotechnical sites – including confined and difficult-to-access spaces. So if you’re looking for a safe pair of hands – give us a call on (07) 3862 2533.